If you’ve ever wondered how some of the everyday plastic items that we use are made, well, the answer is injection molding. This term can be explained as a basic manufacturing process that is used in almost every industry that focuses on making items such as water bottles, containers, toys, trinkets or even automotive body parts.
Just like everything else, injection molding is something that progresses as time goes by, so in today’s article we decided to talk about the five best innovations and trends. If you are interested in learning some more, feel free to keep on reading until the end. Let’s take a look.
Micro Molding
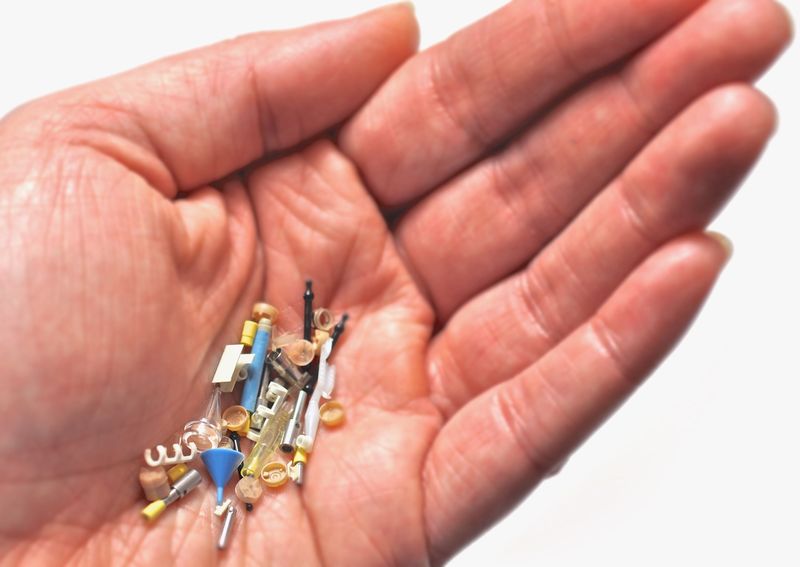
You are probably amazed at the fact that a huge machine such as the one that can be found in the factories can produce an item so small, like a keychain or a phone case, but what if we told you that it doesn’t end there?
Out of all the discoveries and inventions made in this field, micro-molding is the one that probably got the most credit for making a positive change. Machines are now able to construct things on a microscopic level, and even smaller than that in some special occasions. Watch mechanisms and some other parts that we have in our homes and use on a daily basis without even knowing are all the products of micro-molding.
The real revolution however began when this technology started being applied in the medicine field, for creating improved tools and parts so small that the human eye cannot even see them, yet so big that they’re able to save tons of human lives. Sometimes it’s the small details that matter the most.
Eco-friendly materials
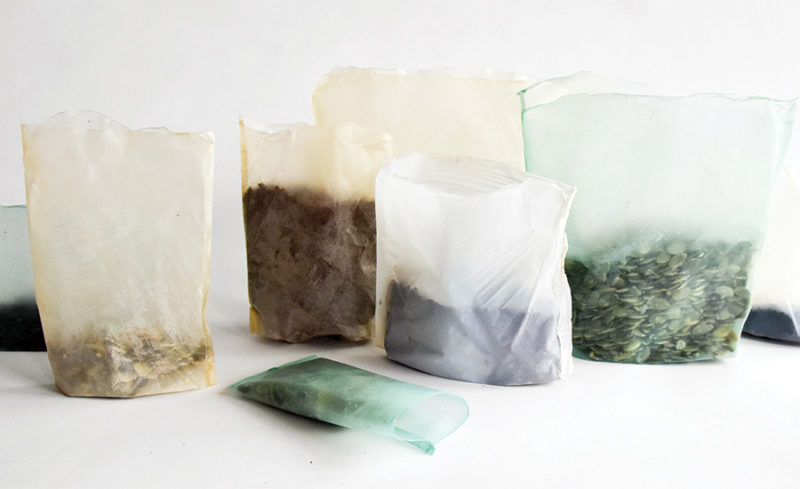
Okay, so all of this is cool, but what happens when the time comes to dispose all of these products which are made out of materials such as plastic? We all know how difficult it is for plastic to decompose into the ground, so how is this contributing to the problem that we currently have with pollution and all that?
Well, the answer is very simple. A few years back, one major innovation in the molding industry allowed factories to use eco-friendly materials, meaning that if you ever want to throw away that phone-case that you’ve been using for so long, it won’t cause that much of a harm to the environment. However, remember that you should always recycle and not just randomly throw away anything, even if it’s made out of an eco-friendly material.
Not only does this allow us to save our environment, but it allows a lot of companies to show their eco-friendly side and get the “green pass”, which is a mark that shows their care for the world.
Robotic quality-inspection
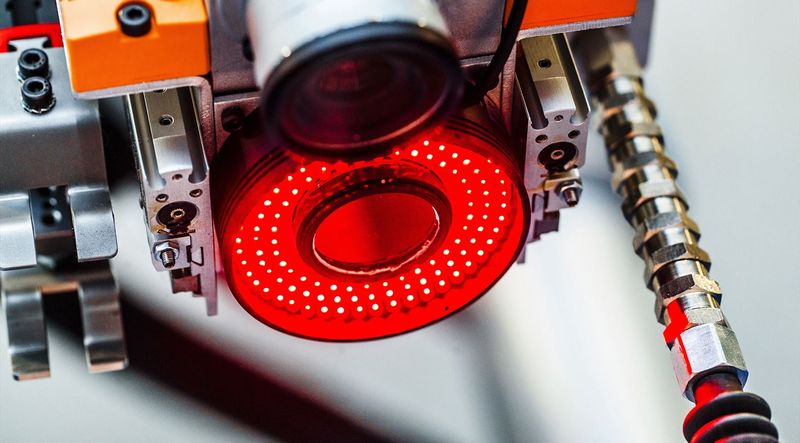
To some people, robots replacing humans in the factories might be a scary thought, and something that reminds them of The Matrix movie where technology takes over the world. However, we assure you that it’s not going to come to that, at least not yet, and with this quality-inspection system, we can see only benefits along the road.
When a certain part is manufactured, no matter what product for, someone needs to check if there are any errors, and if there are, they need to report it so that the machines can be inspected and re-adjusted in needed. Also, that part has to be thrown away.
Now here comes the interesting part. We all know that humans can sometimes make mistakes, so whether if the quality-control guy was taking a nap or they weren’t present that day, there’s still a risk of a faulty part going out of the factory and being shipped for sale.
Luckily, robots have been replacing these people lately, and we know how tireless they are, so we no longer have to worry about faulty parts being shipped.
If you are from China, and you are interested in some quality plastic injection molding services, feel free to check out qmolding.com
3D printing as a part of molding
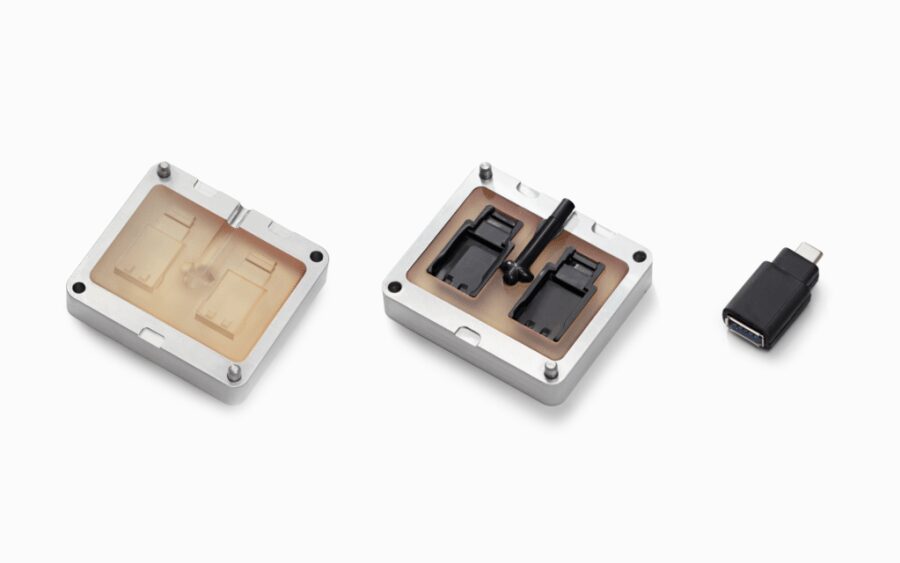
Believe it or not, 3D printing is a lot more useful than people give it credit for. Although most of the older people think that this is just a fancy method for the new generations to make their own toys and action figures, we tend to think otherwise.
3D printing is a great way to make customized items, but not only for fun and entertainment purposes. In the injection industry, people make a lot of custom parts and prototypes that can later be re-produced with the real materials, and it’s just really useful.
Whether you need new tools, parts or just something very specific for your project, you can create it with a 3D printer, and then use it with a real machine to get the perfect product. It is also used for comparison, in way where the creator of the product makes a very detailed version with a 3D printer, and then tests the injection-molding machines to see if they can pull off the same detail-level as the prototype. If not, they can adjust both things until they get to a point where both items will be identical.
Double-shot injection
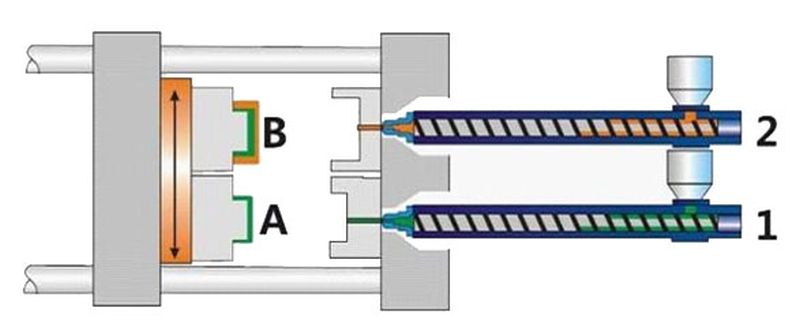
Doubling the efficiency is something that every factory-owner wants, and now they can finally achieve it. Imagine being able to create an item in two different colors, so precisely done and without any errors. Well, as of recently you can, with an innovation called double-shot injection, a process where two cavities are being utilized for the creation of one item.
This can be, and is used for so many different purposes, and although it doesn’t seem like much to the average person, it’s worthy to remember that almost all consumer items that we use on a daily basis were made using the dual-shot injection method.
Conclusion
Whether it’s plastic bottles or complicated parts for sophisticated medical devices, they’re all made in the factory through a method called injection molding. Just like every other field in the modern industry, this one sees a lot of use, and with that we also have many innovations and trends that constantly better the production value. In today’s list, we added the top five innovations that we think have the most impact over the products.