Casting is a process where different items and components are created by using a previously made mold and melted metals. This method has been used for generations, and nowadays many people prefer it before other types of manufacturing.
In this article, we are going to give you more information about the different types of steel molding processes, and we will tell you when they are used. We will also tell you more about the techniques, how things are done, and which metals other than steel can be used. Continue reading if you want to know more about the price of them, advantages as well as the disadvantages.
1. Sand Molding
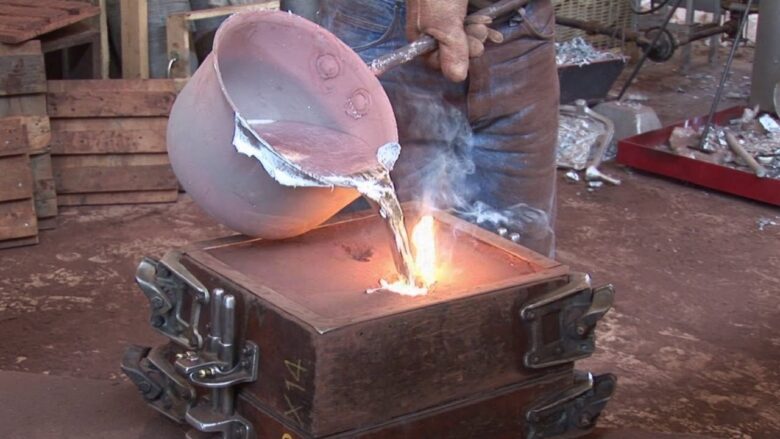
Source: youtube.com
This is probably the most popular process and it is something that has been used for many, many years. The process is simple, first, a cavity is shaped from the natural or synthetic sand. This material is packed around the wood or metal patterns that are previously prepared, and when the pattern is removed, the melted steel is poured into the cavity.
After the metal hardens, the mold is broken, and the cast is removed. That’s about it. However, this is just a basic explanation of the whole process. In manufacturing, there are a lot of other steps in this method, and if they are not followed correctly, there will be mistakes and issues with the final product.
The greatest advantage of sand casting is that it is low in cost, and with it, you can easily create a lot of different types of components. When you produce items in large volumes, it won’t be any issues and you can pour pretty much any type of metal into the cast.
According to DawangCasting, where you can find out more about stainless steel casting when the whole process is done properly, and if items are inspected, then with sand casting, you will be able to create pretty much any type of items you need. The price of the finished products varies depending on the manufacturer, and when you choose the right company, you need to consider all these things.
The negative sides of this process include that it is not practical for items that are supposed to be long and thin, in case you combine steel with alloys, there can be errors and defects, and you will need to resurface the large items. In some cases, there can be a rough surface finish or small cavities, but that depends on the size of the components.
2. Lost wax
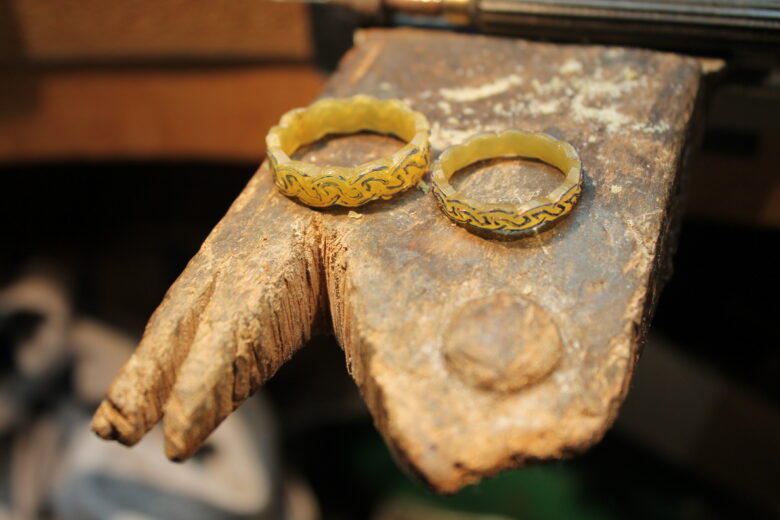
Source: cooksongold.com
Lost wax casting is also called investment casting and the way things are made is that a mold is produced with wax and that disposable pattern is used for each part of the product. It is said that this type of manufacturing has been used for thousands of years, and it may be one of the foundations of the whole process.
Even though this is probably one of the most expensive ways to create molds and finished products, it is also the one that will produce any type of components you may ask for. The way that it works is several layers of wax are put onto the cast until a thick enough mold is created. Later on, the steel is poured into the mold, and when the metal hardens, the mold is broken and remelted.
There are many advantages to this procedure, and the biggest one is that you can create items with a lot of accuracies and any type of design and décor. No matter how complex the component needs to be, and no matter how many small items it needs to have, you can do it all with the lost wax molds. You can pour pretty much all types of metal in it, including ferrous materials. The quality of the finished product will be really high, and you will be able to notice all the details.
Now let’s talk about some of the disadvantages of investment modeling. The first and biggest one is that this process is pricy. It requires a lot of labor, and the patterns and molds that need to be used are expensive. The last negative side of this operation is that there is a size and weight limit, so you cannot create parts that are too big.
3. Metal Molding
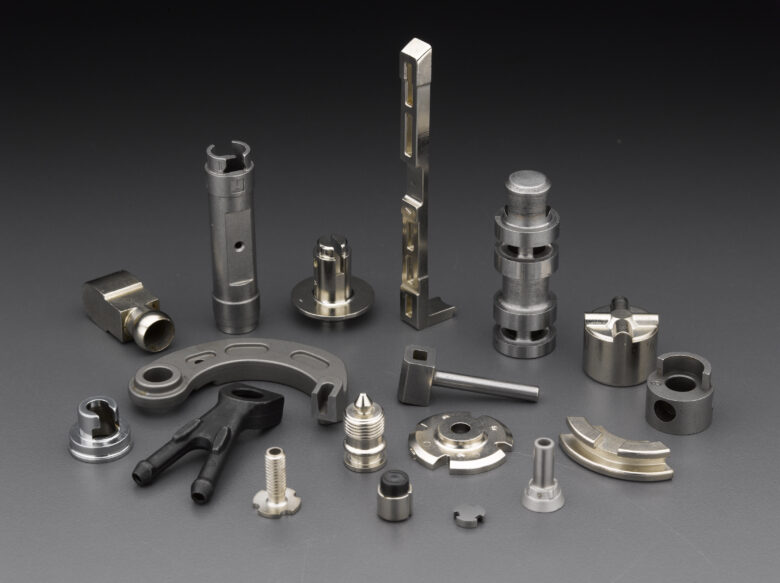
Source: wikimedia.org
The last procedure we are going to talk about is called metal or die modeling. The way things are produced is that the molding is made using high pressure. The method is relatively similar to the lost – wax molding, but there are some things that are different between the two.
To create new objects, the professionals first melt the needed metal, and then they pour it into the mold. The last step is applying pressure until all the cavities are filled. Once the metal is completely cooled off, the mold is removed. There are several different types of metal molding, and depending on the type of metal and the items needed, professionals choose the best one.
The advantages of this process include the uniform design of all the parts that are going to be produced, and when the operation is done, there will be little to no need for post-casting finishing. However, the size of the components you can create is limited, and you need to think about the weight as well. The cost can be higher than the rest of the operations, but it is said that even though you may need to invest more, you are also going to get better products.
These are some of the ways that you can manufacture steel components by using molds. Choosing the right type depends on your needs, and if you want to create parts or products made of steel, it is always best to consult with a professional manufacturer before you choose the right type. Note that your budget, the size of the elements, as well as their details will make a difference, so write down the things that you need and approach the professional service with your list of needs before choosing the molding type.