With the innovation and growth of 3D printing technology, the aerospace industry has seen a shift in jet engine design, operation, and optimization. This transformation is spearheaded by the diverse approaches of 3D-printed jet engines that aim to address the performance and fuel efficiency of the components amongst other things.
When it comes to fuel efficiency, from managing complex geometries for improved aerodynamics and weight reduction to the construction of lightweight structural elements and managing thermal properties with advanced cooling channels, rapid prototype manufacturing, particularly in the creation of 3D-printed jet engine parts, has emerged as a game-changer.
The advent of rapid prototype manufacturing fostering unprecedented advancements in design, production speed, and ultimately, fuel efficiency. This revolutionary method enables the production of intricate jet engine parts. The precision and customization which is characteristic of 3D printing are not only integral for optimal performance but reduced environmental impact as well. Therefore, it marks a significant milestone on the evolutionary path of the aviation system.
Enhance Aerodynamic Dynamics by 3D-Printed Turbine Blades
Traditional manufacturing techniques often fail to take into full context the intricacy of turbine blade designs and that is why they are not able to maximize aerodynamic efficiency. With 3D printing, there is an increased focus on the precision with which complex geometries can be manufactured. This new development is great for optimizing the shapes of turbine blades in a manner that their aerodynamic features such as contoured airfoils are best utilized.
Amongst the many advantages of 3D printing is the production of hollow lattice structures present in the turbine blades. These structures intend to decrease the weight of the blades and, therefore, improve the aerodynamic performance by enhancing heat dissipation and air circulation. Ultimately, it all leads to an impact on the thrust efficiency and, as a result, better fuel efficiency for the jet engines.
Furthermore, 3D printing expands on the customization potential of turbine blades as it strives to meet the operational requirements of the blades more effectively. Engineers now have the resources to tweak the geometry to optimize it in the hope of achieving both robust structural integrity and aerodynamic efficiency.
Reducing Aircraft Weight by 3D-Printed Structural Components
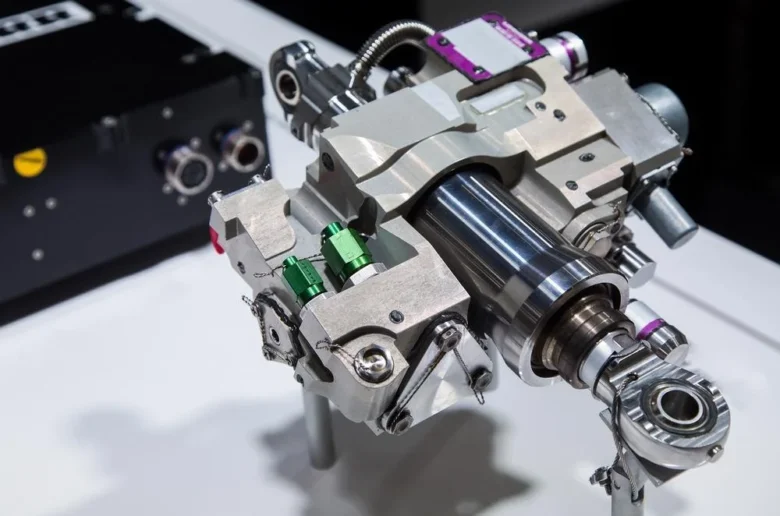
Fuel consumption is directly dependent on the weight of the aircraft and, therefore, there is a requirement for lightweight structural components that are more than capable of performing. 3D printing is an extraordinary alternative when it comes to achieving this. While conventional manufacturing techniques make use of subtractive processes that remove excess material and generate more waste, with 3D printing an additive construction process is followed. Lightweight layers are used to optimize the material consumption and are intended for efficient performance.
The previously mentioned lattice structures are also integral additions to these structural components. By adding the appropriate brackets and supports, the lattice design can be experimented with so that it can strike the right balance between weight and strength. 3D printing also facilitates the customization of the design so that only the most necessary features are included so that the weight can be considerably reduced. For instance, the creation of interior panels has made various traditional elements redundant leading to lower weight.
With 3D printing, load-bearing structures such as fuselage frames and wing ribs can also be experimented with to find an optimal weight that still has the required strength. These structures are subjected to varying stresses throughout the flight and, therefore, customization is needed to manage this stress distribution in a way that it could lend the component the best strength. The reduction in the aircraft weight can also happen with material composites such as high-strength alloys that are usually lightweight but strong. As a consequence of reduced weight, you can expect to spend significantly less on fuel.
Enhancing Thermal Management with 3D-Printed Intricate Cooling Channels
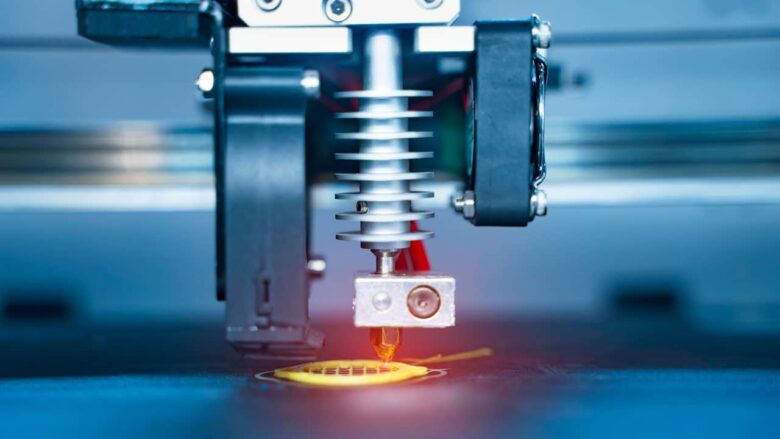
The cooling channels found within components of traditional jet engines are not developed enough to dissipate the heat properly. They don’t take into account the complex structures that are characteristic of cooling channels. 3D printing on the other hand can help design and produce components that are suited to meet the thermal demands that vary from position to position in a jet engine.
Turbine blades have to function in extreme temperatures with a wide range of variations and that is why intricate cooling channels are a necessity when it comes to jet engines. In particular, serpentine channels are vital for the operation of the cooling system. They carry the cool fluid through different areas of the engine to assist in dissipating the generated heat.
As their name suggests, they have a snake-like structure that helps them achieve their intended purpose. They have to be designed in accordance with the composition of the blades and should be able to manage critical temperatures well. Such conformal cooling channels are essential to adapt to the contours of the engine. This is because certain locations require more cooling than others and identifying the amount of fluid required is the key to ensuring that no cooling is wasted.
The importance of engineering cooling channels that take into serious consideration thermal management can’t be stressed enough. Thermal efficiency is directly linked with fuel efficiency because it translates into how much fuel is converted into mechanical work. With better thermal efficiency, more fuel is being utilized and less is going to be wasted.
Customized Fuel Nozzles for Precise Combustion
Traditional jet engine designs are limited in their execution and may struggle to facilitate proper combustion. Therefore, there was a need for more suitable fuel nozzles for precise combustion. That gap was bridged by the invention of 3D printing. These designs vary based on the specific engine configurations and that is what makes them so adaptable. Tailoring the combustion process is integral when it comes to enhancing fuel efficiency.
Fuel nozzles are narrow structures and, therefore, they have to be designed with even more care than some of their other counterparts. Its complex geometries, such as accurately calibrated injector ports and swirl patterns, should be manufactured in a way that facilitates better fuel discharge. Additionally, a properly designed nozzle would have greater control over the fuel-air mixture and would allow more sustained combustion.
3D printing is also flexible in the way in which it can help integrate composite materials with heat-resistant characteristics. Combustion has to be considered in light of the different extreme conditions that it might find itself in. Therefore, utilizing these properties is where the solution to most of the combustion issues often lies. With 3D printing, you can obtain durability and longevity which means that there would be less need for maintenance as combustion can be damaging to the engine at times if not done properly.
The iterations that accompany the 3D printing process can be valuable because they help refine the internal features of the fuel nozzles. Not every nozzle is the same and this technique takes into consideration this very fact. As a result, the performance is carefully customized to the demands of every specific fuel nozzle and the fuel efficiency reflects the same.
Conclusion
The execution of 3D printing in the aerospace industry has shown an upward trajectory in recent years and it is probably because of the multiple benefits it lends. There is no need to be shackled by the same old limitations of the traditional manufacturing processes of jet engines when 3D printing can change the complete landscape of how the components are designed.
With this technique, you can expect efficient aerodynamics, thermal and combustion dynamics. All of which are closely associated with fuel efficiency. For jet engines, this efficiency is critical in deciding what the performance output would be and how much expenses would be incurred. Therefore, its optimization is a significant stepping stone when it comes to the growth of the jet engine design.