When it comes to protecting products during shipping and storage, shrink wrap and stretch film are two of the most common packaging materials used today. But what exactly sets them apart?
While shrink wrap and stretch film may seem interchangeable at first glance, they each serve very different purposes. Stretch film is designed to stabilize pallet loads for transport, while shrink wrap creates a tight seal around individual items or small bundles of products.
Understanding the key differences between shrink wrap and stretch film can ensure you select the right material for your business’s specific needs. This guide examines stretch film and shrink wrap in depth, including their composition, applications, and methods for use.
We’ll also provide tips for choosing between the two and finding the right stretch wrap suppliers to meet your requirements. With the right information, you’ll be equipped to make informed packaging decisions that protect your products and support your business goals.
What is Stretch Film?
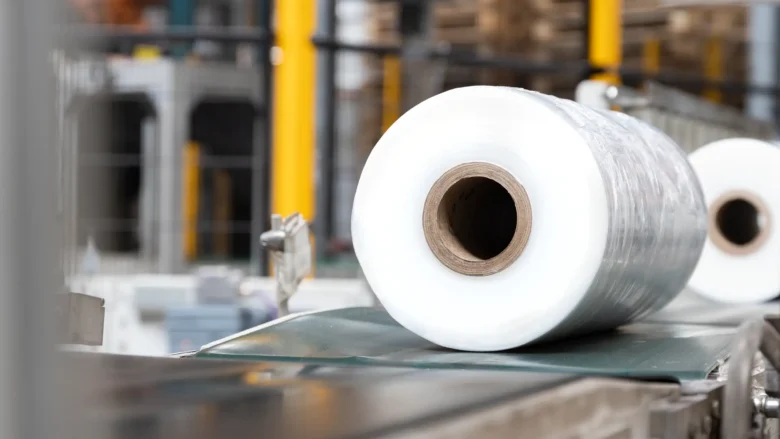
Stretch film, also known as stretch wrap or pallet wrap, is a versatile and widely used packaging material designed primarily to stabilize pallet loads for shipping and storage. It is typically made from linear low-density polyethylene (LLDPE) or other similar polymers.
Key Properties and Composition
- Elasticity: Stretch film is highly elastic, which allows it to be stretched and wrapped tightly around pallet loads. This elasticity ensures that the film conforms to the shape of the load, providing stability and security during transit.
- Transparency: Most stretch films are transparent or semi-transparent, allowing for easy visibility of the goods being wrapped. This transparency is particularly useful for inventory management and security checks.
- Thickness (Gauge): Stretch film comes in various thicknesses, commonly measured in microns or mils. Thicker films offer increased puncture resistance and load stability, making them suitable for heavier or irregularly shaped loads.
- Adhesion: Stretch film possesses a degree of cling or adhesion to itself, which helps keep the layers securely bound together during wrapping. This property contributes to load stability.
Main Uses and Benefits:
- Load Stability: The primary purpose of stretch film is to secure and stabilize palletized loads. It prevents items from shifting, collapsing, or falling during transport, reducing the risk of damage.
- Dust and Moisture Protection: Stretch film acts as a protective barrier against dust, dirt, and moisture. This is especially valuable for goods that require protection from environmental elements.
- Cost-Efficiency: Stretch film is a cost-effective packaging solution. It minimizes the need for additional strapping or materials to secure pallet loads.
- Ease of Application: Stretch film can be applied manually, semi-automatically using stretch wrapping machines, or fully automatically in high-volume operations. This flexibility makes it suitable for businesses of all sizes.
Stretch film is a versatile, elastic packaging material used predominantly for unitizing pallet loads. Key properties like cling, transparency, and elasticity make it an effective solution for stabilizing and protecting goods during shipping and storage. It provides businesses with an affordable and easily automated packaging option.
What is Shrink Wrap?
Shrink wrap, a versatile packaging material, is distinct from stretch film in its composition and primary applications. Shrink wrap is designed to create a tight, protective seal around individual items or small bundles of products. It is commonly made from polyolefin or PVC (polyvinyl chloride).
Key Properties and Composition of Shrink Wrap
- Shrinkability: The hallmark feature of shrink wrap is its ability to shrink tightly around products when exposed to heat. This heat-induced shrinkage conforms the wrap to the contours of the items being packaged, creating a snug and protective covering.
- Transparency: Similar to stretch film, shrink wrap is often transparent or semi-transparent, allowing for product visibility. This transparency is especially valuable in retail packaging, where product display is crucial.
- Thickness (Gauge): Shrink wrap comes in various thicknesses to accommodate different product sizes and weights. Thicker shrink wrap provides enhanced durability and protection.
- Sealing Properties: Shrink wrap can create a secure, tamper-evident seal, offering protection against unauthorized access or tampering.
Main Uses and Benefits of Shrink Wrap
- Product Display: Shrink wrap is widely used in retail packaging for its ability to showcase products clearly while providing protection against dust and handling.
- Waterproofing and Dust Protection: Shrink wrap offers excellent protection against moisture, dust, and environmental elements, making it suitable for safeguarding a variety of goods.
- Tamper-Evident Packaging: The shrink-wrapped seal provides a clear indication if a product has been tampered with, adding a layer of security.
- Food Packaging: In the food industry, shrink wrap is commonly used for packaging perishable items, ensuring freshness and hygiene.
- Reduced Packaging Material: Shrink wrap often requires less material compared to other packaging methods, contributing to cost savings and reduced environmental impact.
Shrink wrap is a versatile packaging solution that conforms tightly to products when heat is applied, creating secure retail packaging that displays items attractively. Its customization options for thickness and transparency enable businesses to tailor it to their specific merchandising and durability needs. Shrink wrapping provides efficiencies through minimal materials usage along with protection against dust, moisture, and tampering. With advantages for display, security, and efficiency, shrink wrap is a flexible solution with broad applicability across industries.
Key Differences Between Stretch and Shrink Wrap
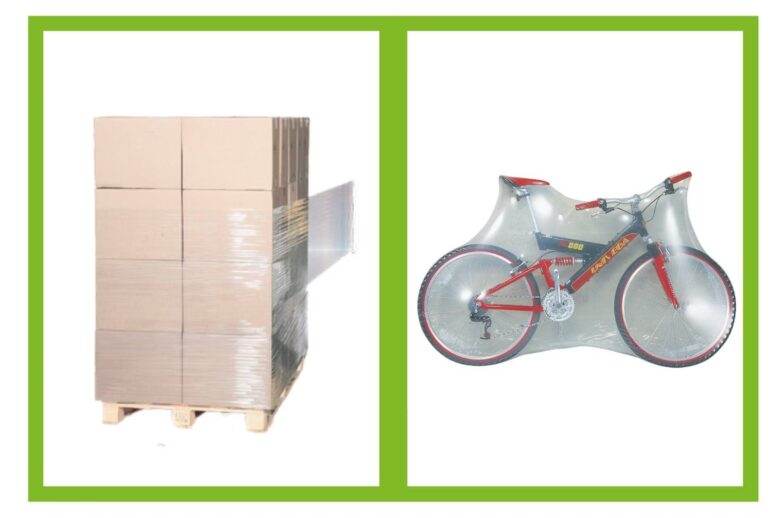
Stretch film and shrink wrap may share some common characteristics as packaging materials, but they serve distinct purposes and are applied differently. Here are the key differences that set them apart:
Stretch Film | Shrink Wrap |
Primarily used for stabilizing pallet loads, stretch film is designed to secure and protect multiple items or products on a pallet. It ensures load stability during transportation and storage. | Shrink wrap, on the other hand, is employed to tightly wrap individual items or small bundles of products. Its primary role is to provide protection, display, and tamper-evident packaging for these items. |
Stretch film’s primary function is load stability. It prevents items on a pallet from shifting, collapsing, or falling during transit. It focuses on securing the entire load as a whole. | Shrink wrap excels at product presentation. It tightly conforms to the shape of the individual items or bundles, showcasing them effectively while also offering protection and tamper resistance. This makes shrink wrap ideal for retail packaging. |
Stretch film can be applied manually, where workers wrap the film around the pallet loads by hand. It can also be applied using semi-automatic or fully automatic wrapping machines for higher efficiency. | Shrink wrap requires heat for application. It is either applied manually using a heat gun or heat-sealing equipment or passed through a heat tunnel for automatic and uniform shrinking. |
Stretch film is typically made from linear low-density polyethylene (LLDPE) or similar polymers. Its composition emphasizes elasticity and strength. | Shrink wrap is often made from polyolefin or PVC (polyvinyl chloride). Its composition is optimized for heat-induced shrinkage and conformity. |
Understanding these key differences is essential for businesses to select the right packaging material for their specific needs. Whether you require load stability through stretch film or product display and protection via shrink wrap, making the correct choice can significantly impact your packaging efficiency and product presentation.
Choosing the Right Packaging Material
When picking stretch wrap versus shrink wrap, think about what you’re packaging and what you need to accomplish. Ask yourself – am I shipping full pallet loads or individual products? If it’s pallets, stretch wrap is the go-to for stability. But if you want pretty retail packaging, shrink-wrap shapes to products nicely.
Also, consider whether load stability or stylish presentation matters more. Stretch wrap keeps things locked tightly in place. Shrink wrap shows off products with a nice tight fit. You’ll also want to think about efficiency – are you wrapping manually or using automated equipment? Do the cost-benefit for your volume.
When to Choose Stretch Wrap
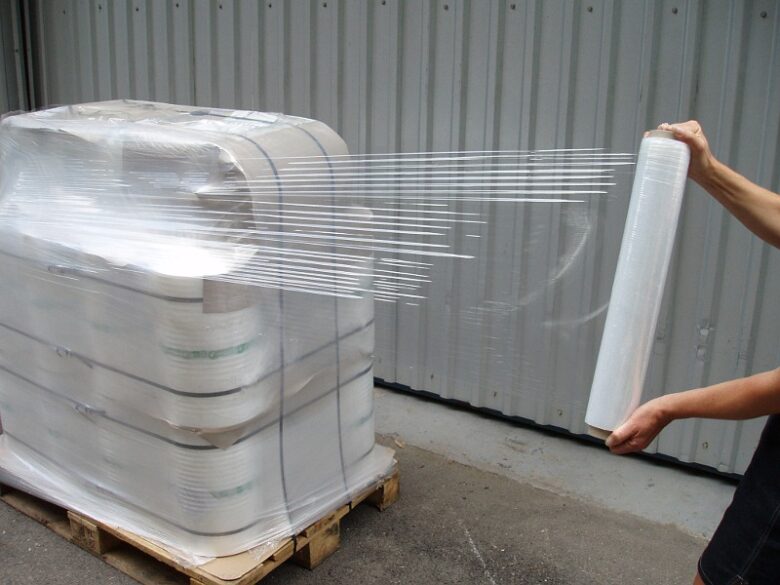
Stretch wrap is the move when you need serious load stability for shipping and storage. It bonds everything together so your pallets won’t collapse or shift around. It’s also great when you’re moving stuff long distances across supply chains. Stretch wrap keeps everything secure so your goods arrive intact.
And don’t forget it protects against dust, dirt, and moisture. So for anything that needs to stay pristine inside and out, turn to stretch wrap.
When to Choose Shrink Wrap
Shrink wrap shines when you want beautiful retail packaging that makes products pop on the shelf. It hugs every contour nicely and tight so customers take notice.
It also makes a great moisture and dust barrier to keep contents safe from the elements. So if you need serious waterproofing and protection, shrink wrap has you covered. And don’t forget the food industry. They love shrink wrap to keep food fresh and on display at its best.
Finding the Right Packaging Supplier
Picking the perfect packaging supplier is key. You want a company you can rely on long-term that really cares about your business. Make sure they have plenty of inventory in stock so you never run out when you need materials fast. And be sure to compare pricing. Getting quotes from a few places is a normal and great practice to do. You need to know that you’re getting a good deal.
Also, look for great customer service. You need a supplier who can answer questions and help resolve any issues that pop up quickly. Check delivery times and lead days too – your supplier should be able to fulfill orders and ship promptly to keep your packaging operations humming.
The last thing that you should check is their reputation. Look for positive reviews and signs that they have a track record of making customers happy. That’s the kind of partner you want by your side.