There are several approaches to construction project management. Each approach has pros and cons, but you can turn all the odds in your favor by adopting the right ones. One such approach is using construction management software like Bridgit to automate the project tracking process.
A feasible approach and project management tool can save you time and money. This will help you to gain clients’ trust and business reputation in the construction industry.
This post will list the four major approaches to construction project management.
4 construction project management approaches
It’s the project manager’s job to decide what construction project management approach to use. Every approach differs from the other, depending on the project’s nature. So using only one approach for all construction projects might not be a good idea.
Here are the four major approaches:
1. Waterfall
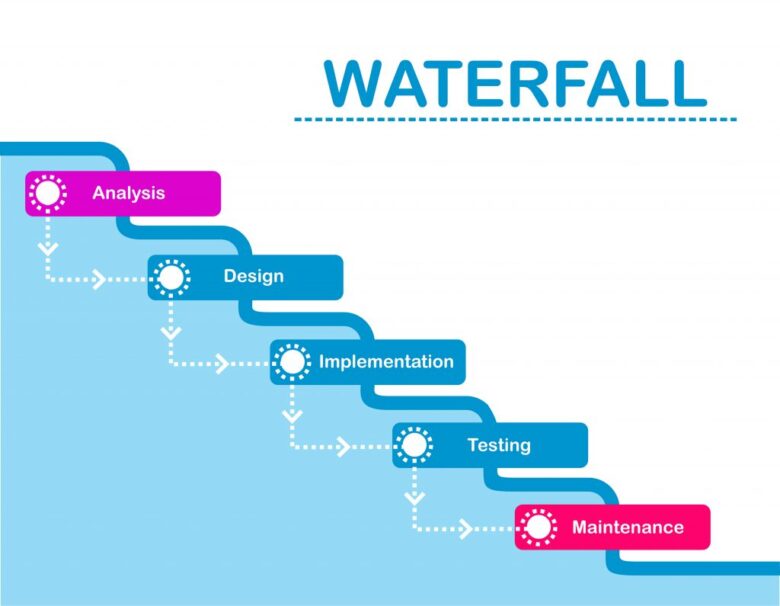
It’s the traditional project management approach in the construction industry. As the name suggests, the waterfall approach is a simple, top-to-bottom way of managing a construction project.
There are five major steps in waterfall project management:
Requirement gathering
The project manager and the client hold meetings and share details regarding the project. During the meetings, the client shares the project requirement with the manager and elaborates every detail.
Although the client might not have enough technical knowledge, a construction consultant or a civil engineer accompanies the client during the requirement gathering phase.
Similarly, the project manager allows them to join the meeting because it builds clarity and trust among the stakeholders.
Design
Architects and designers analyze the requirement document and start designing the construction plan in the form of blueprints. A blueprint is a blue-colored sheet on which architects draw a detailed structure and mention important details and calculations.
Besides, you can use modern construction software and create digital building structures instead of traditional blueprints.
Implementation
After designing, project managers and contractors decide on the capacity plan and work on procurement. Once the resources are arranged, the project manager allows the teams to start working. Similarly, the contractor goes to the site to begin the construction.
Verification
Senior management checks the requirement and capacity documents. The client also validates the requirement plan before the final approval.
The documents are then sent to the relevant government department for verification. These authorities pass the construction bill only if the documents fulfill the rules and regulations of the project.
Maintenance
During the construction, the project manager and engineers keep inspecting the project. In addition, a testing team stays active after the project closure to find and fix incomplete tasks.
2. Agile
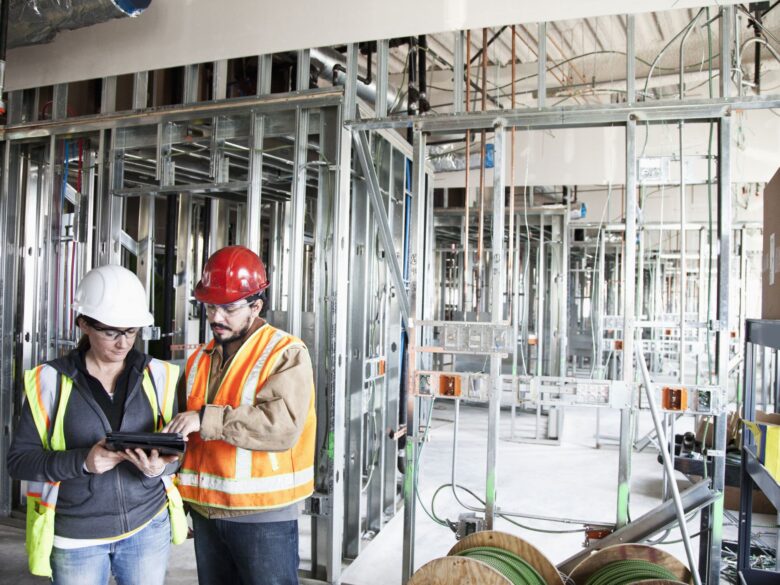
Agile construction project management imitates today’s software development approach. This methodology breaks the project’s milestones into smaller, easily manageable parts.
Since construction projects require several months to complete, estimating resource utilization is difficult. Your project can face delays if you fail to schedule resource management.
For example, there is limited equipment available. Due to time constraints, team A couldn’t finish its tasks, and team B also delayed its tasks due to insufficient resources. Now, you can only improvise and rent more equipment if you have more than enough budget, which is rare.
So what are you going to do? The agile approach helps you create segments of milestones that the software can track throughout the project’s lifetime. You can also collect regular feedback and measure performance while the teams work on completing those smaller segments based on priority.
The financial team can also speed up their processes and make better decisions from the smaller units. That ensures:
- Better resource utilization – The project manager can optimize equipment usage and save fuel, maintenance, and repair costs.
- Productivity – Better resource utilization can boost productivity throughout the project.
- Profitability – No surplus usage of equipment can save cost overruns.
Furthermore, the project manager receives employee feedback and takes action to improve team management by communicating with them.
That way, the team members stay motivated and do their best to complete the project within the allocated budget and time.
3. Critical chain

The critical chain approach is the longest dependency chain among tasks and resources. This approach is different from the critical path in project management.
Critical chain is undoubtedly exhausting, but it can reduce the project duration by 40% using the same resources.
Generally, it’s assumed that task B can’t be initiated if task A is incomplete because of the chain effect, and the resources remain available. But that’s usually not the case in the construction industry.
The critical chain method helps you detect resource allocation errors and scheduling loopholes. Additionally, you can detect where variability exists in resource utilization.
Following the critical chain approach to construction project management, you can make changes that remain in the project execution.
However, critical change requires a smart mindset while planning and scheduling the construction project. Since it’s challenging to critically analyze resource management before construction, project managers might not want to follow this approach.
4. Lean construction management
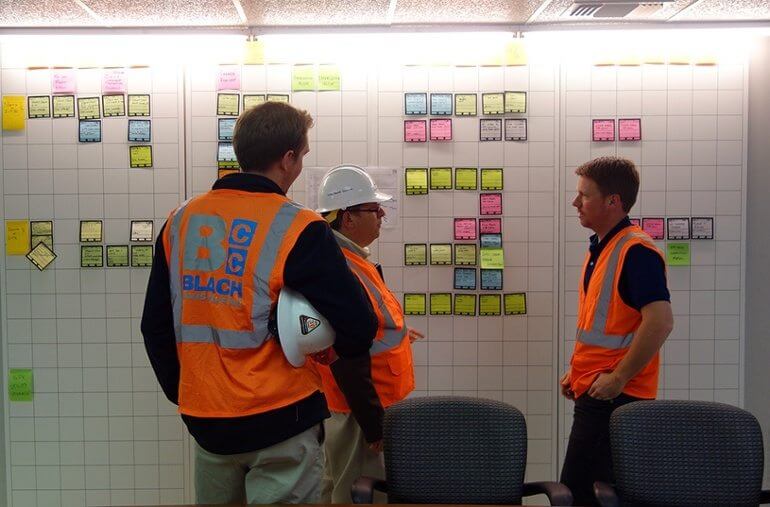
The lean construction management approach adds value to the project by efficiently executing the client’s requirements. In this approach, the project manager continuously gathers client feedback and improves work efficiency.
When you get real-time reviews during the project, you can understand the construction requirements in a better way.
The project manager ensures that the workflow remains streamlined. But focusing too much on every requirement and client’s feedback simultaneously might disturb the ongoing construction.
The lean construction management approach does the planning phase in reverse order. The planning begins with the client’s project goals. When you understand the project goals, you can easily gather as many requirements as you want.
You can also determine the possible risks associated with the project which might hinder the progress. Therefore, you have enough time to make a risk mitigation strategy and prepare a reliable construction plan.
This approach can save you time and money because the planning document has every detail directed towards the project goals. Also, lean construction management removes communication barriers from the stakeholders by providing a common channel.
Thus, you can avoid:
- Bottlenecks
- Delays
- Miscommunication
However, this approach is difficult to apply because project managers, contractors, and planners might have to give up their roles and work as a facilitator instead.
Conclusion
Construction companies use different approaches to execute projects. They might not follow the new construction project management approach due to adaptability issues. As a result, they face project delays and cost overruns.
The four construction project management approaches are waterfall, agile, critical chain, and lean construction management. So choose the most feasible approach for your next construction project and manage it efficiently.