Many things could cause accidents in warehouses. The stored heavy items could fall, or the forklift trucks that shift stock could injure someone. Therefore, it’s essential that warehouse owners put in place safety measures to ensure that the work environment remains harmless to the employees. As stated in the Health and Safety Work Act 1974, employers have a responsibility of ensuring that employees are safe.
In this guide, we tell you of some of the things in a warehouse that could cause accidents and what to do to prevent that from happening.
The Floors
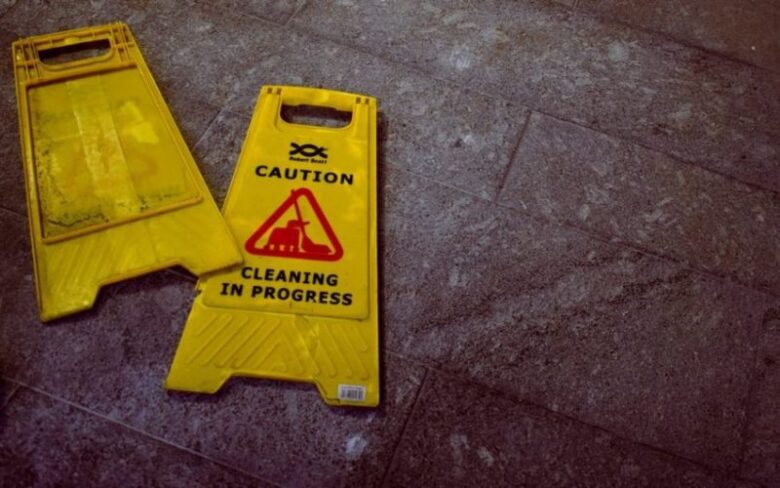
Slips and trips cause the majority of accidents in these buildings due to slippery floors. You should, therefore, take adequate measures to make sure that the floors are always dry and clear of any obstacle that might cause a fall such as trailing wires and boxed stocks, among others. When doing the risk assessment, you should start with flooring and consider what to do to minimize or if possible, completely prevent risks.
Risks include spillage, which cannot only cause a person to slip but it’s also a potential fire hazard. If you have wires passing across a part of the floor, you should also think of what to do to prevent them from causing slips and trips while at the same time finding ways to minimize damage on wires caused by passing vehicles.
If you suspect there’s a risk of tripping and slipping, install anti-slip measures. For example, you could place an anti-slip tape to areas where stock is carried most. Also, ensure that everyone in the warehouse wears suitable footwear. And check to confirm that the edges of elevated areas are safely made. It’s also imperative that you ensure sufficient lighting in your building.
Vehicles
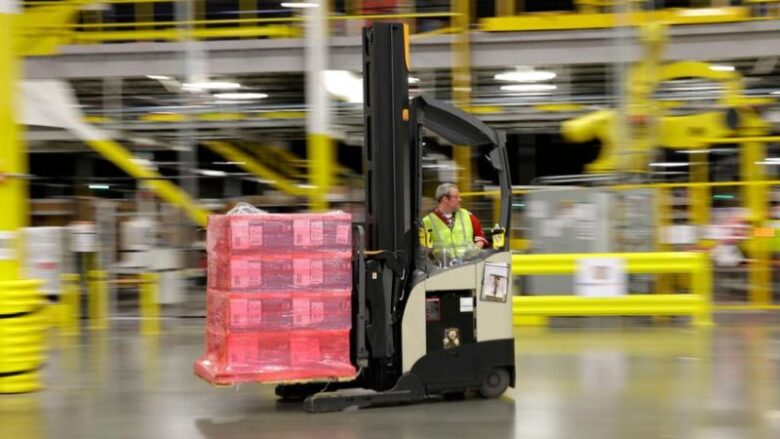
Vehicles operating inside a warehouse are of many types including forklift and pallet trucks. The key safety measure when it comes to vehicles is to make sure that the drivers know how to operate them. If you are not sure, check with The Approved Code of Practice from the Health and Safety Executive as it outlines the proper guidelines for training of forklift drivers.
However, the vehicles can also cause some injuries if carelessly driven. You should, therefore, put in place strict rules to be followed when driving these vehicles in the warehouse. It’s also crucial that you regularly take the vehicle for servicing to ensure its suitability for the job. And again, check for blind spots and inform drivers to be wary of them.
Signage and Equipment
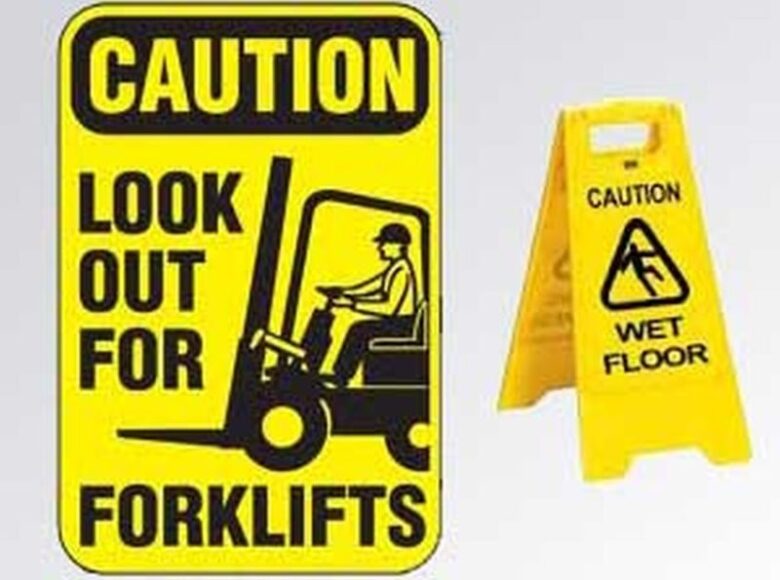
Signs facilitate communication in the warehouse and help as well as remind workers to know of hazards and what they should do to avoid accidents. They include warning signs such as dangerous machinery is used or toxic chemicals. Ensure that everyone reads and understands the signage and also place them in easily noticeable areas. If you are placing one on fire exit doors, ensure that it’s illuminated to promote visibility as suggested by tradesignship.co.uk because in darker areas its better to opt for more reflective signs so they are more visible in low light.
And when it comes to equipment, it’s your duty to supply the employees with enough working tools, and that includes personal protective equipment such as hand gloves, protective footwear, eye goggles, and highly visible jackets. If you need more PPE information you can check on: www.anbusafety.com they are one professional personal protection equipment supplier.
Racking
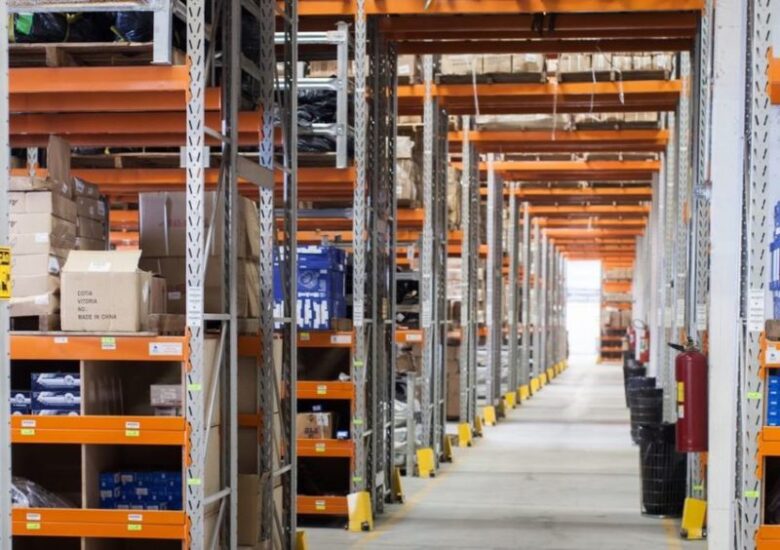
How and where you store your items matters a lot. First, have a competent person to fit the racks to prevent collapses. Then consider protecting the racks to avoid them from being damaged for instance they may be accidentally hit by a moving vehicle. You should also inform the staff on the dangers of climbing on the racks and ensure that you put rules for that. You might also want to avoid overloading your racking system with too heavy materials, in fact, it’s advisable that you place the heavy load on the ground. Lastly, it’s also wise that you invite a Storage Equipment Manufacturers Association (SEMA ) rack inspector to come to inspect your racks and racking parts regularly. For further information, visit rackingspares.co.uk.
Handling Stock
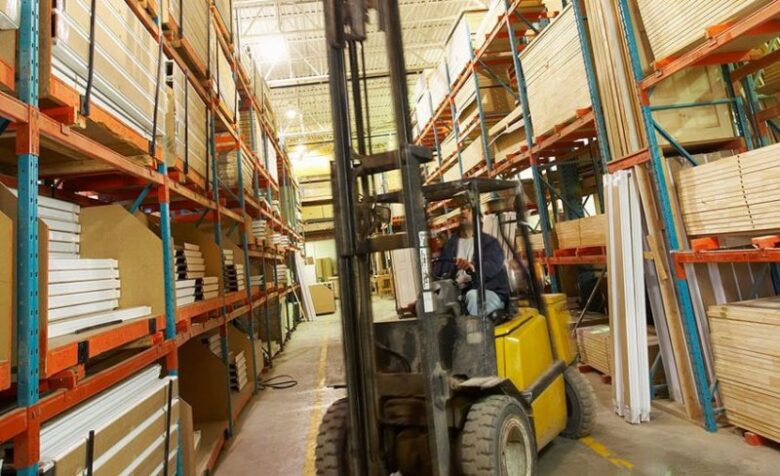
Practice safer methods of handling stocks often to prevent your workers from getting injuries caused by lifting, carrying, and shelving heavy loads. Instead of workers doing such tasks manually, you can consider mechanical processes such as using lift trucks and trolleys as much as possible. However, when the only option is manual lifting, then consider doing a risk assessment of the area as well as the job itself.
Training
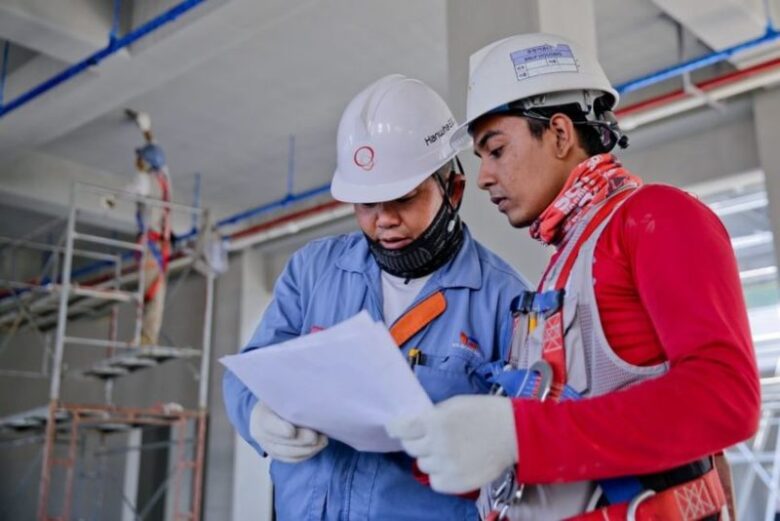
Anyone working in the warehouse should receive sufficient training. If you have any new employee, ensure that they are well trained and informed of the safety measures and abide by the set rules and regulations. Make sure they know how to handle the equipment and machinery and also check to ascertain they know what to do should there be a fire. You can check out The TRH-Group for more details.”
Warehousing work activities create many health and safety risks. For this reason, the warehousing industry reports a high number of fatalities every year. But those statistics could significantly reduce if simple safety measures are followed. Use these safety tips and a health and safety management system to keep yourself and everyone operating in the warehouse from getting injuries. Learn even more on health and safety systems here.