Sheet metal cutting is an essential process in metal fabrication, used to transform raw metal sheets into finished products. While the cutting process itself is crucial to the success of a fabrication project, ensuring safety during cutting is equally important. Fabricators must adopt best practices and safety measures to prevent accidents, injuries, and damage to equipment. The importance of safety in sheet metal cutting cannot be overstated, as it not only protects workers from harm but also ensures that the end product is of high quality.
In this article, we will explore the best practices for fabricators to follow when cutting sheet metal, including safety measures that should be taken to ensure the well-being of workers and equipment, and the importance of proper training and equipment maintenance. By following these best practices, fabricators can ensure that their sheet metal cutting operations are both safe and effective, resulting in high-quality finished products.
Why Safety is Important in Sheet Metal Cutting?
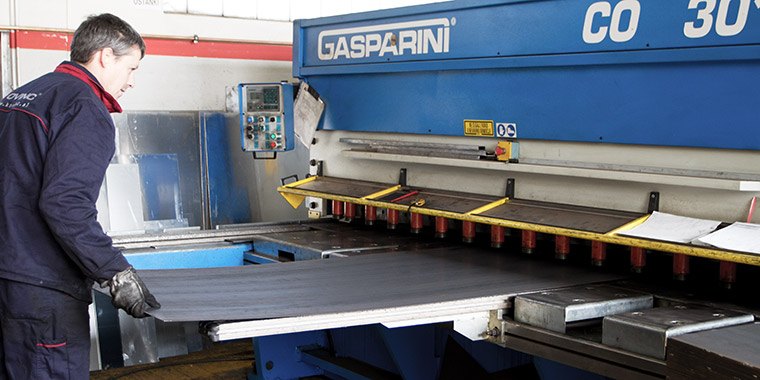
Sheet metal cutting is an essential process in the fabrication industry, but it can be a hazardous task for workers. It involves the use of sharp tools and heavy machinery, which can cause severe injuries if proper safety measures are not taken. That’s why safety is a top priority in sheet metal cutting, and fibbers must implement best practices to ensure a safe workplace.
One of the main reasons why safety is important in sheet metal cutting is to prevent accidents and injuries. Workers can face various hazards during the cutting process, such as cuts, burns, and hearing damage. These injuries can result in significant medical expenses, lost wages, and decreased productivity. By prioritizing security, fabricators can minimize the risk of accidents and injuries, protect their workers, and save on costs.
Another reason why security is essential in sheet metal cutting is to comply with regulations. Occupational Safety and Health Administration (OSHA) and other regulatory agencies have established protection standards that must be followed in the workplace. Failure to comply with these regulations can result in fines, legal action, and damage to a company’s reputation. By prioritizing safety, fabricators can comply with regulations and ensure a safe workplace for their employees.
Moreover, security is crucial in sheet metal cutting to maintain the quality of the products. Accidents and injuries can lead to errors in the cutting process, resulting in products that do not meet the required standards. By prioritizing security, fabricators can ensure that the products they produce meet the required quality standards, leading to satisfied customers and increased business success.
Best Practices for Fabricators in Sheet Metal Cutting

- Proper Training: Fabricators must ensure that their workers have received proper training on sheet metal cutting, including the safe use of tools and machinery. Workers should also receive regular refresher courses to keep their skills up-to-date.
- Use Personal Protective Equipment: Fabricators must provide workers with personal protective equipment (PPE) such as protection glasses, gloves, and earplugs to minimize the risk of injury.
- Machine Maintenance: Regular maintenance of machinery is essential to prevent accidents and ensure the quality of the products. Fabricators should inspect their machines regularly, perform repairs as needed, and replace any worn-out parts.
- Implement Safety Procedures: Fabricators must establish and implement safety procedures for sheet metal cutting. This includes protocols for handling and storing materials, operating machinery, and responding to emergencies.
- Identify Hazards: Fabricators should conduct a hazard analysis of their sheet metal cutting processes and identify potential risks. This can help them develop strategies to mitigate these risks and prevent accidents.
- Monitor Workers: Fabricators should monitor their workers’ behavior and enforce security procedures. This can include regular safety audits, providing feedback, and addressing any unsafe practices.
Why it’s Vital to Use Modern Technology in Sheet Metal Cutting
Using modern technology for sheet metal cutting is essential for several reasons. First and foremost, modern techniques offer superior precision, accuracy, and repeatability, ensuring high-quality cuts and consistent results. This level of precision is crucial for industries that require intricate and complex designs.
One of the key modern ways to achieve efficient sheet metal cutting is through laser cutting. Laser cutting utilizes a high-powered laser beam to cut through various types of metal with exceptional accuracy and clean edges. Its versatility allows for intricate shapes and designs, making it a preferred choice in industries such as automotive, aerospace, and electronics. If you are in need of professional help in this department or you operate in one of these industries you can find a reliable partner in zltechlaser.com.
Another modern method is waterjet cutting, which employs a high-pressure stream of water mixed with abrasive particles to cut through the metal. This technique is highly versatile, offering the ability to cut through various thicknesses and materials without generating heat-affected zones.
Plasma cutting is another advanced technique that utilizes ionized gas to melt and sever the metal. It is particularly suitable for cutting thicker sheets and offers fast cutting speeds.
CNC machining, utilizing computer-controlled machines, allows for precise and automated cutting of sheet metal. This technology enables efficient production and consistent results.
Importance of Proper Training and Equipment Maintenance
Proper training and equipment maintenance is crucial in ensuring safety during sheet metal cutting operations. Improper use of cutting equipment and lack of knowledge can lead to accidents, injuries, and damage to equipment. Workers should receive comprehensive training on safe cropping procedures, handling of materials and equipment, and use of personal protective equipment. In addition, equipment must be properly maintained to prevent mechanical failures, which can cause accidents and injury. Fabricators must establish maintenance schedules to ensure that equipment is regularly inspected, repaired, and replaced as needed. By prioritizing proper training and equipment maintenance, fabricators can minimize risks and ensure the safety and success of their sheet metal trimming operations.
Training programs for workers

This is essential in ensuring the safe and effective operation of sheet metal pruning equipment. Workers must be knowledgeable about the risks associated with sheet metal cutting, as well as the proper use of cutting equipment and personal protective equipment. Training programs should cover topics such as safe handling and storage of sheet metal, machine operation, lockout/tagout procedures, and emergency response. These programs can be delivered through in-person instruction, online courses, or a combination of both. Regular training and refresher courses should be provided to ensure that workers are up-to-date on best practices and safety measures. By providing comprehensive training programs, fabricators can promote a culture of safety and minimize the risk of accidents and injuries.
Conclusion
Safety should always be the top priority when it comes to sheet metal cutting in metal fabrication. By implementing best practices and safety measures, fabricators can protect their workers, equipment, and the quality of the finished product. It is important to properly train workers on safe-cutting procedures and to maintain equipment to prevent accidents and injuries. Fabricators should also utilize appropriate personal protective equipment and take the necessary precautions to prevent hazards such as fire, electrical shock, and mechanical failures. By taking these measures, fabricators can create a safe working environment and ensure the success of their sheet metal cutting operations. Ultimately, a commitment to safety not only protects the well-being of workers and equipment but also leads to higher-quality finished products and increased customer satisfaction.