There is a myriad of reasons that lead to I. If a factory is beginning a delicate operation, the supervisor has to issue instructions in each stage during the beginning, each time for four hours. The instruction usually takes around 20 minutes. The workers in charge of the task will have nearly a minute of idleness in a single day as they are given instructions at least three times per day.
In a manufacturing plant, the standard hours workers work 50 hours a week. He earns $10 per hour. If the plant experiences an issue with power failure, and the employee is idle for 10 hours each week, then the employee has to work only 40 hours, and the rest of 10 hours are his idle time. The 40-hour cost is then considered direct labor costs, while the additional cost for the idle hours must be classified as indirect labor expense and is included in the overhead cost.
What Exactly Is Idle Time?
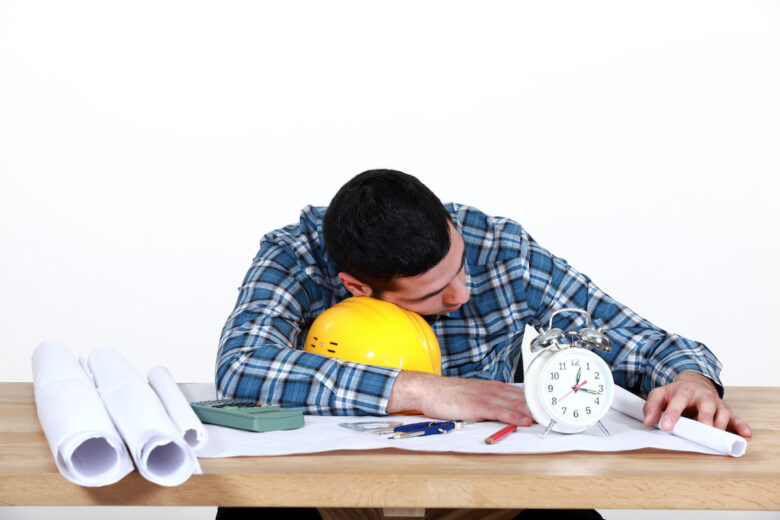
Idle time is when the asset is available and ready; however, it isn’t doing any productive work. This is the reason idle time can be called waiting time.
Idle time refers to the time the machine is waiting to input material. It’s a worker in the office waiting for their internet connection to be restored. A truck is on a construction site in the waiting room for an excavator move to reach its desired location. The mechanic is waiting for the circular saw to be available to complete his work.
You need to know and monitor idle time because it reveals gaps between actual output and your theoretically maximum productivity level. Simply put, every minute your employee or machine is not working is a minute that you lose productivity.
However, there is no way to run with 100 percent effectiveness. A certain amount of inactivity is inevitable. Any manager aims to limit inactivity and never eliminate it. Eliminating idle hours is nearly impossible and could only be considered in closed, high-tech, highly-automated systems.
What Is the Difference Between Idle Time and Downtime?
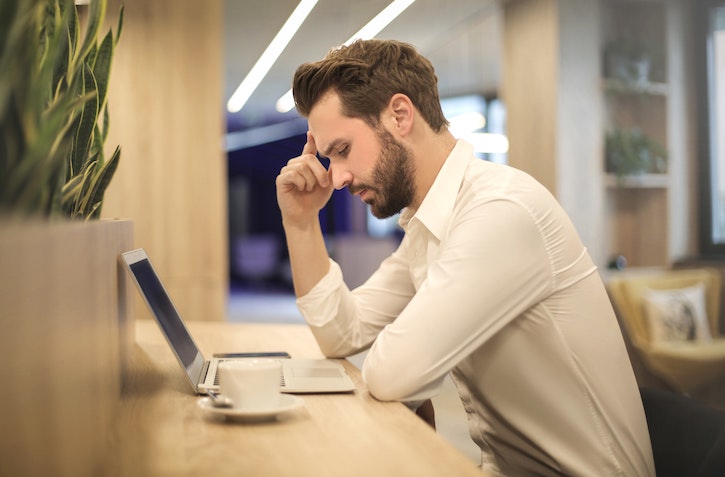
Maintenance professionals often misunderstand the words idle times and “downtimes. While both terms indicate assets that are “out of order,” they differ in their meaning. The term “downtime” refers to any time that equipment in the facility is not available to use. Unlike idle time caused by problems unrelated to asset functionality, downtime means an asset is not in working order. This is why the difference between the two terms is why the asset fails to perform.
Although equipment failures are the most common cause for downtime, they’re by no means the sole reason. Facilities managers typically plan downtime to delegate the preventive maintenance (PM) tasks to maintenance technicians in the non-peak hours of production or when business is not in session. This is why strategic, operational managers monitor idle time and downtime differently.
The Causes of Idle Time
The reasons for idle time encompass all of the possible reasons for work to suddenly and abruptly stop. The reason behind the idle time is typically outside the employee’s control and may or might not be in the control of management.
1. Production Line Issues
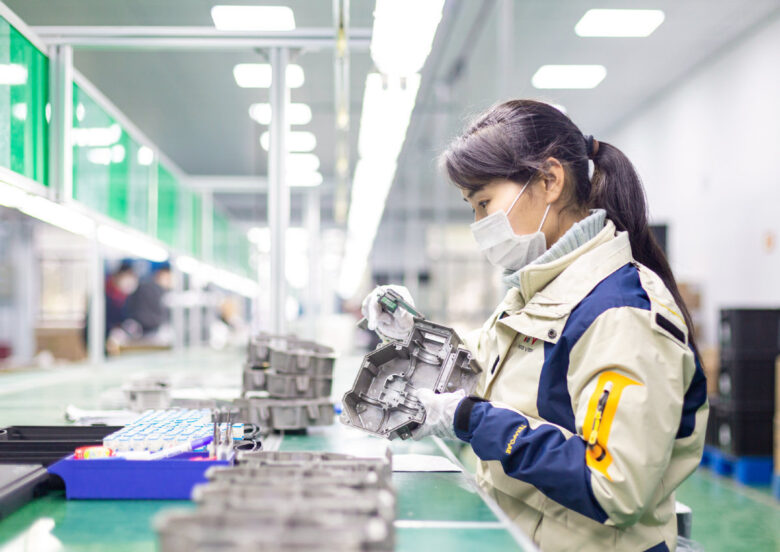
There is also inactivity when they face production-related problems. Manufacturing facilities usually have idle time as employees are waiting for raw materials. The longer the needed materials to arrive, the idler time the business endures. In addition, power outages or outages, as well as delayed instructions for production, can cause machines to go offline, leaving workers inactive.
2. Temporary Stoppage of Work
Another reason for inactivity can be a temporary stoppage, which the company’s management forces. This can happen when, for instance, stock storage facilities are operating at total capacity and cannot accommodate any more goods. Thus, management can temporarily suspend production until some of the inventory has been either sold or removed.
3. Worker Inefficiencies
Workers are not machines, and certain workers perform better than the rest. They require breaks to keep from burning out. Certain inefficiencies are due to new employees going through an adjustment process. To combat worker inefficiencies, you should improve your onboarding process and create an environment where everybody is required to take on their burden.
4. Equipment Malfunctions
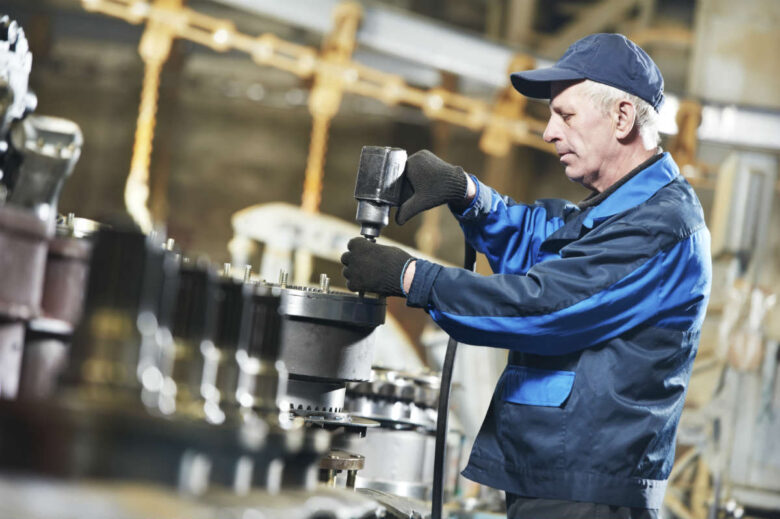
Unexpected machine breakdowns could cause severe operational problems. Maintenance departments should utilize the CMMS system and implement an ongoing maintenance plan for all high and medium-priority assets.
In addition, you can utilize the maintenance planner skills to instruct the personnel responsible for conducting maintenance on industrial equipment. Maintenance planners create documents that cover training, maintenance, and reporting procedures.
5. Process Design
The processes are usually designed to involve multiple different stages in production. In the present, the time taken by the product to move between one and the next step in the production line might represent one of the causes for the typical inactivity and cannot be removed.
6. Lower Efficiency
Sometimes idle times, it could be caused by manpower that has low efficiency. A worker may not be efficient at the beginning of their workdays, have health problems, or entirely intentionally. Management typically tries to limit intentionally low efficiency as it could affect productivity in the future.
7. Administrative Failures
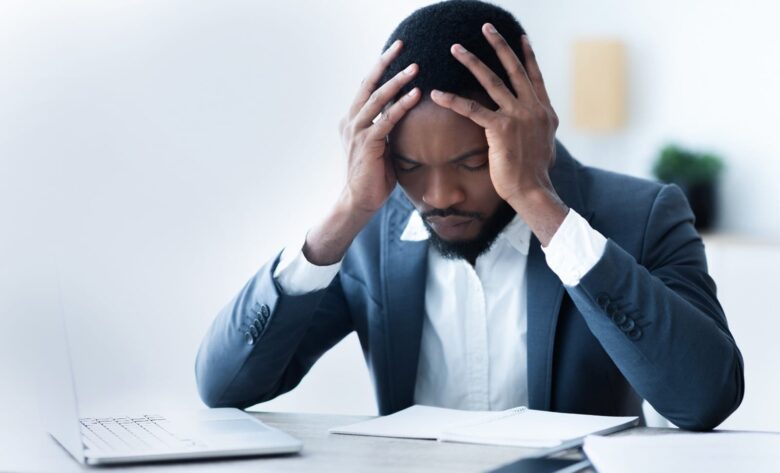
Insufficient planning and poor decision-making could lead to a waste of time working. For instance, the warehouse could hire new workers because they anticipate an influx of customers for a new product. If, however, its initial projections for sales are not met, and the warehouse cannot meet its expectations, it will suffer over time due to the need for more employees than are needed in the timeframe.
8. Market Dynamics
Unforeseen shifts in market dynamics, such as the emergence of a new rival, can cause an excessive amount of idle time. In such cases, businesses are forced to cut back on production due to a drop in consumer demand. Other market conditions that can result in idle time include strikes by employees, cyclical fluctuations, and economic issues like the COVID-19 supply chain problems.
9. Natural Disasters
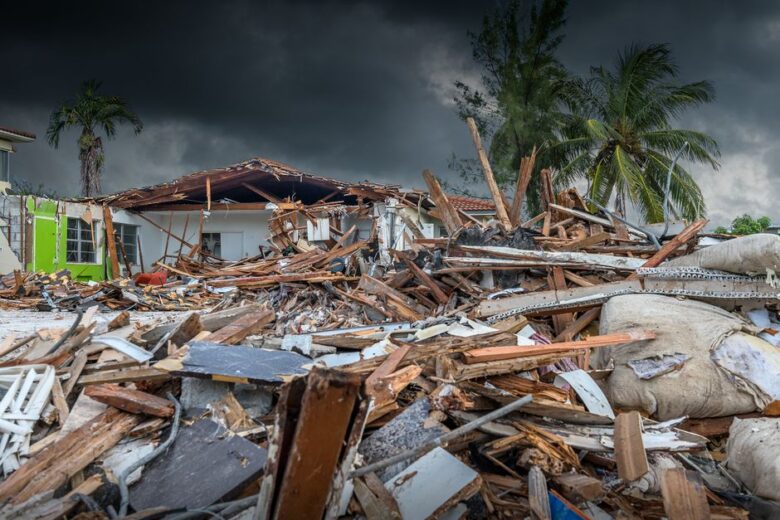
Also, if you work in industries that rely on specific weather conditions – mining transportation, trucking, or shipping -weather events can significantly impact facility productivity. The only thing that employees can do in these situations is to wait out the storm. The delay in travel caused by adverse weather events typically triggers delays for all the organizations involved in the supply chain.
Final Words
Idle time refers to when assets do not perform their function even when they are in use. Companies can reduce idle time and reduce costs by identifying reasons behind unplanned equipment failures and adopting strategic solutions. The best method of tracking the patterns of idle time is to use the use of computerized maintenance management software (CMMS).