The world of screen printing is an enthralling blend of art, business, and craftsmanship. Venturing into this vibrant realm requires more than just an artistic vision; it demands a profound understanding of the right tools, ensuring that every creative impulse is translated with precision and clarity onto your chosen medium.
Having the essential supplies on hand doesn’t merely guarantee the quality of each print, but it’s a beacon signaling success and professionalism in your business. In this guide, we’ll delve deeper, shedding light on the core tools and equipment that will accompany you as you embark on this colorful and rewarding journey.
Screens and Mesh
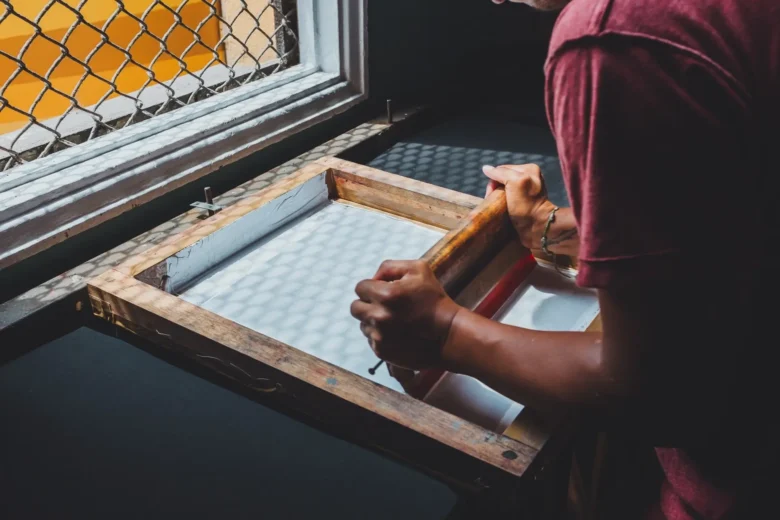
Source: ynvisible.com
At the very heart of screen printing, pulsating with importance, are its screens and mesh. Acting as the foundational stencil, they pave the way for you to seamlessly transfer your envisioned designs onto various substrates, ranging from fabric and paper to even more unconventional materials.
The mesh count, an often overlooked aspect, is pivotal in determining the fineness of detail and the volume of ink that can pass through. A lower mesh count, with its larger openings, readily permits more ink, making it the go-to choice for bold, impactful designs. On the other hand, a higher count intricately weaves tighter openings, favoring more detailed designs.
It cannot be stressed enough that the quality of your screens is of paramount importance. A robust, well-tensioned screen, such as silk printing screens, is a guarantee of uniform ink distribution, leading to impeccable results. Since screens, like everything, can degrade over time, a strategic investment in top-notch quality from the get-go is not only wise but cost-effective in the long run.
Squeegees and Blades
In the art world, just as brushes are indispensable to painters, squeegees are the unsung heroes for screen printers. They are the gatekeepers of ink application, ensuring flawless consistency across every inch of your design.
The choice of squeegee material, while seemingly trivial, can significantly influence the print outcome. For instance, while rubber boasts a softer nature, making it versatile across various ink types, polyurethane stands out with its remarkable durability.
Moreover, the shape of the blade profoundly impacts the ink distribution. While round blades lean towards a gentler touch, square blades lay down a more substantial ink deposit. Ultimately, the blade’s choice will intertwine with the specific needs of the design and the printer’s personal preference.
Inks and Emulsions
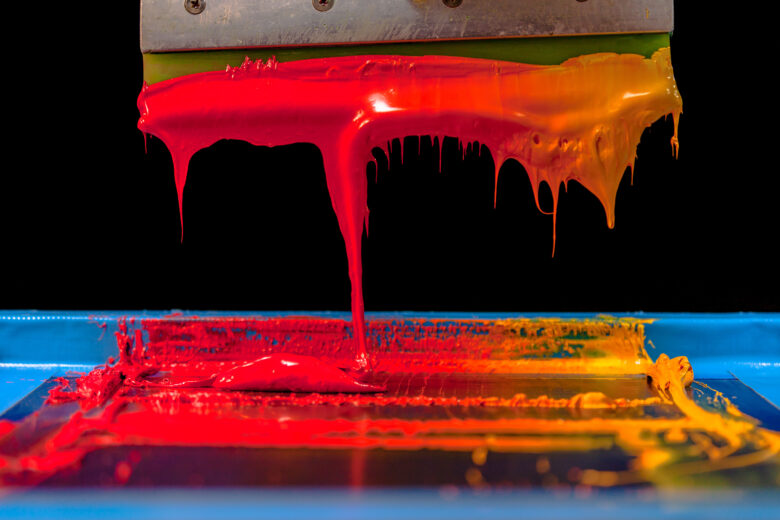
Source: fespa.com
In the realm of screen printing, the selection of ink can be a defining moment. Screen printing inks showcase a spectrum, from water-based inks, celebrated for their eco-friendly attributes and soft tactile feel, to plastisol, renowned for its durability and vibrancy, and discharge inks, which pre-emptively remove the shirt’s original color before layering a new hue. The substrates you aim to print on, coupled with the finish you desire, will dictate your ink choice.
In contrast, emulsions serve as the silent workhorse, meticulously creating the stencil on the screen. Upon exposure to light, these emulsions undergo a transformation, hardening in exposed areas while the shielded regions remain soft and pliable. This intricate dance results in the design ‘negative,’ the very blueprint that allows the ink to pass through in exact patterns.
Exposure Units and Light Sources
Achieving a razor-sharp design demands the impeccable curing of the emulsion. This is where exposure units step into the limelight.
These specialized devices harness various light sources, be it LED, halogen, or fluorescent, to methodically harden the emulsion. When navigating through options, consider factors like your anticipated work volume, the complexity and detail in your designs, and of course, your allocated budget.
Drying and Curing Equipment
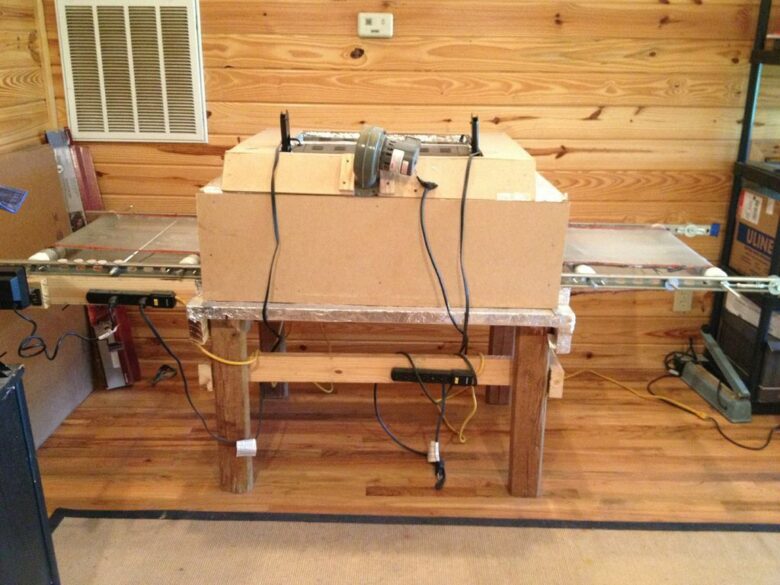
Source: pinterest.com
The post-printing phase, often underestimated, is pivotal. Once a design is imprinted, it needs a thorough setting. Missing the mark here can lead to heartbreak in the form of smudged or prematurely faded prints.
The arsenal of tools at your disposal includes conveyor dryers, ideal for processing high volumes; flash dryers, which specialize in rapid spot curing; and heat presses, which fortify the design’s longevity on the material. It’s imperative to maintain consistent temperatures throughout to ward off the risks of under or over-curing.
Registration Tools
In the colorful world of multi-color prints, the unsung hero ensures perfection is registration. Precision tools like registration marks, pins, and clamps are the magicians behind ensuring that each color aligns flawlessly, creating a harmonious print. This is not just a skill, but an art, and mastering it is non-negotiable for achieving professional, crisp, and vibrant designs.
Cleaning and Reclaiming Supplies
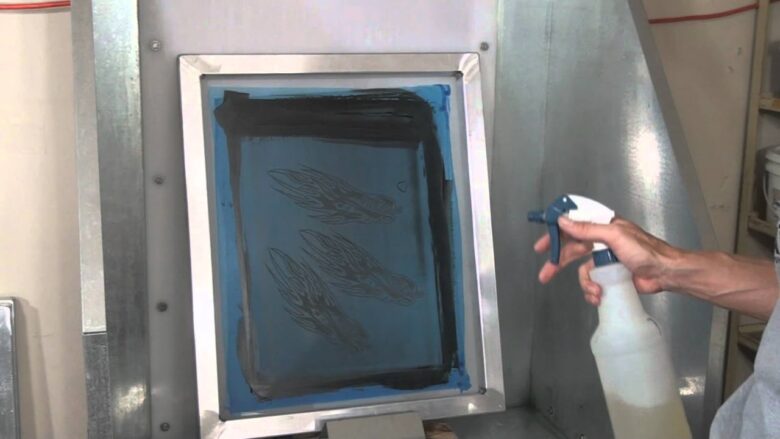
Source: m.youtube.com
The longevity of screens hinges on meticulous maintenance. For them to be reused, a thorough cleaning regime is essential. Specialized chemicals break down lingering ink residues, while scrub brushes and pressure washers assist in the reclaiming process. In today’s environmentally-conscious world, it’s worth exploring eco-friendly alternatives, ensuring your operations have a minimized environmental footprint.
Workstations and Print Tables
Ergonomics, often brushed aside, plays a pivotal role in bolstering productivity and maintaining health. Adjustable tables and ergonomically designed workstations act as guardians, preventing physical strain and ensuring that the printing process remains seamless. Furthermore, an organized, clutter-free space is not just pleasing to the eye but also amplifies operational efficiency.
Exposure Calculator and Test Prints
The exposure calculator, a nifty tool, is your guiding light in determining the optimal exposure time for your screens. When coupled with test prints, they become a dynamic duo, ensuring that every print boasts optimal ink density and unerring color accuracy, drastically reducing potential errors.
Safety Gear and Ventilation

Source: lboro.ac.uk
Safety, a cornerstone of any workspace, is non-negotiable in the screen printing universe. Personal protective equipment like masks, gloves, and aprons act as shields against inadvertent ink splashes and chemical exposure.
Simultaneously, robust ventilation systems are essential to ensure that harmful fumes are expelled, guaranteeing a workspace that’s not only productive but also health-conscious.
Additional Supplies and Resources
Beyond the primary toolkit, there are other indispensable gems like pallet tape, scoop coaters, and screen racks, each enhancing the overall printing experience. It’s also beneficial to forge collaborations with reputable suppliers and perpetually stay attuned to the ever-evolving industry trends, ensuring continuous growth and innovation.
Conclusion
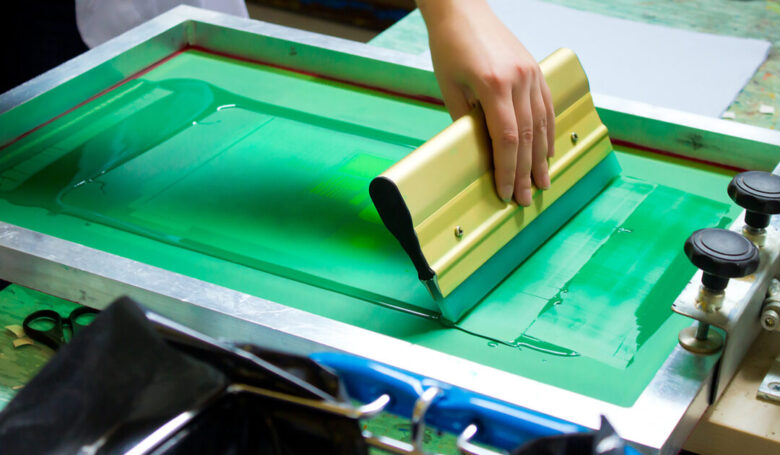
Source: fullpressapparel.com
Embarking on the exhilarating journey of screen printing is akin to orchestrating a symphony, blending artistry with intricate technical know-how.
By meticulously investing in top-tier tools and resources, you’re not just ensuring impeccable prints, but you’re also laying a robust foundation, setting your business on an upward trajectory of success and unparalleled innovation. Embrace every nuance of this journey, and here’s to printing masterpieces!