The containment of hazardous liquid chemicals – whether flammable/combustible, explosive or corrosive substances – is required for the protection of the environment. They also pose different health risks to humans, such as irritation, sensitization, and carcinogenicity. Spills of certain chemicals can cause irreversible damage to biodiversity and contaminate the soil, the air, and the water.
It is crucial that the storage units – tanks or containers – need to be appropriately engineered and installed, whether you want to rent a container or a tank or buy new ones. They must have double walls so that secure containment of materials will be provided for both the personnel and the environment. They are also for the protection of the substance that is being stored.
Therefore, they are strictly regulated by the Occupational Safety and Health Administration (OSHA) and the Environmental Protection Agency (EPA). Such storage tanks or containers can be found on various sites, including coal and nuclear power plants, as well as different industrial, commercial, educational, and medical facilities.
So what are the most important things when it comes to storing such chemicals?
Proper Labeling
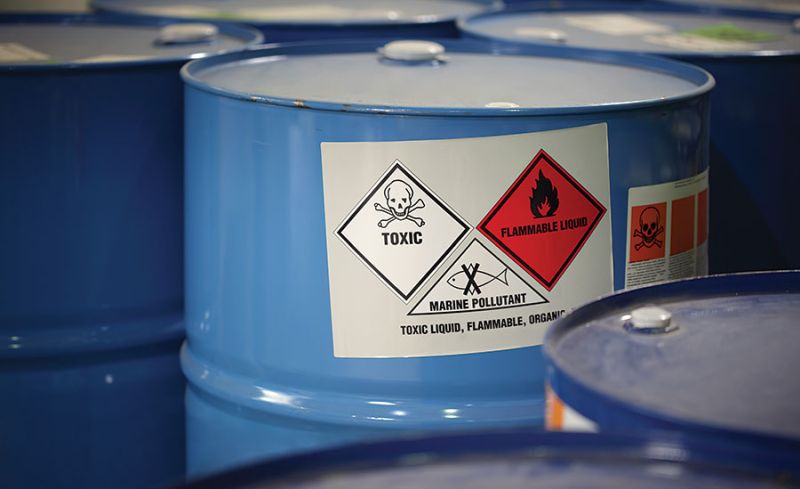
In this case, one does judge the book by its covers. In the chemical industry, suitable labelling is everything. Labels are essential since they provide information to the workers, or anyone who handles, uses, stores, and transports the specific chemical.
However, they are limited by design in the amount of information they can provide, so they are usually accompanied by Safety Data Sheets (SDSs), which are a more complete source of information.
The chemical manufacturers and importers are required to assess the hazards of the chemicals they produce or import, and to prepare labels and safety data sheets on them so that their downstream customers will be familiar with the risks and the correct ways to store and handle these substances.
Trained Employees
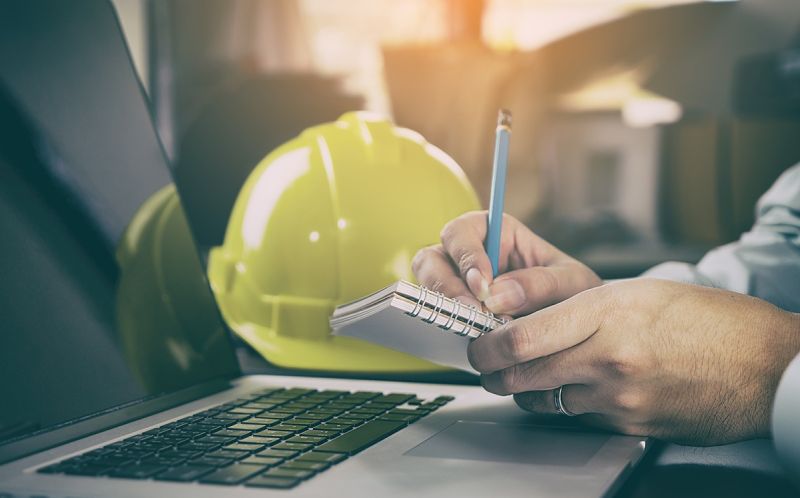
As previously mentioned, the employers must have labels and safety data sheets for their exposed staff, and to continuously train them to appropriate handling of the chemicals, so that accidents and injuries can be prevented.
Leaks and spills that are in the immediate proximity of the storage tanks must be addressed without any delay in order to reduce the risk of slipping the workers, as well as other types of microbiological, thermal, or caustic injuries. Of course, some chemicals have long term health effects, so workers must be aware of any kind of unwanted exposition to these substances.
Also, the staff must adhere to safe handling practices when refilling and dispensing the storage tanks and to be on alert that hot work (any work that involves using fire- or spark-producing tools, or other work that produces a source of ignition, such as welding, cutting, brazing, grinding, etc.) should not be performed on the storage tank or container unless they are completely emptied, and the remaining vapours of the hazardous substance are eliminated.
High-Quality Storage Tanks
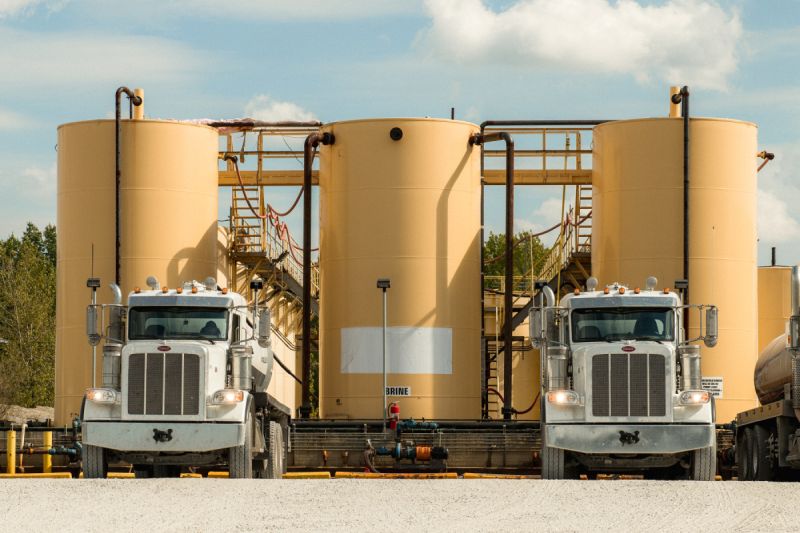
source:rollingstone.com
The specific type of container or tank that will be used depends on the properties of the particular material that is being stored; whether it is toxic, flammable, contaminated, and so on. For example, for diesel, according to NFPA 30, storage requirements are based on whether the liquid fuel is combustible or flammable as assessed by the so-called “fuel flash point” which is the lowest temperature at which the fuel will ignite in the presence of an ignition source. The combustible liquids are defined by NFPA 30 as having a flash point equal to or greater than 100F (37.8C), while flammable liquids as having a flash point less than 100F (37.8C).
It is crucial that the storage units – tanks or containers – that are being used to be appropriately engineered and installed. They must have double walls so that secure containment of materials will be provided for both the personnel and the environment. They are also for the protection of the substance that is being stored.
Namely, the inner tank dome overlaps outer tank sidewall and prevents rainwater, snow and debris from entering into the containment basin. There could be a built-in secondary compartment. Also, they need to be equipped with spill guards against accidental leaks and with fast response system for determination of the level of liquids stored inside them. This helps so that any leaks don’t go unnoticed. Such storage tanks can be found at adlertankrentals.com.
Some tanks are equipped with emergency relief venting that will release internal pressure, in case the tank is exposed to fire. Others have special insulation and tank heating systems for temperature-sensitive stored liquids, complete with heat tracing.
Adequate Location
The location of a particular tank or container can be deemed as permanent, transitional, or temporary, depending on their purpose and duration of storage. They can be installed above the ground, buried underground, or situated within a storage tank vault that is above or below grade, or within a storage tank building.
ontainers or tanks must be positioned away from any source of direct heat as many substances are sensitive to a change of temperature. Tanks must be located in an area where there is no risk of collision with vehicles because some substances can catch fire if they get in touch with a hot engine. Also, they need to be positioned in a place that is least likely to result in contamination of sewage, underground waters, or soil and are a subject to minimum separation distances from buildings, farming grassland, public ways, as well as property lines.
Responsible Management
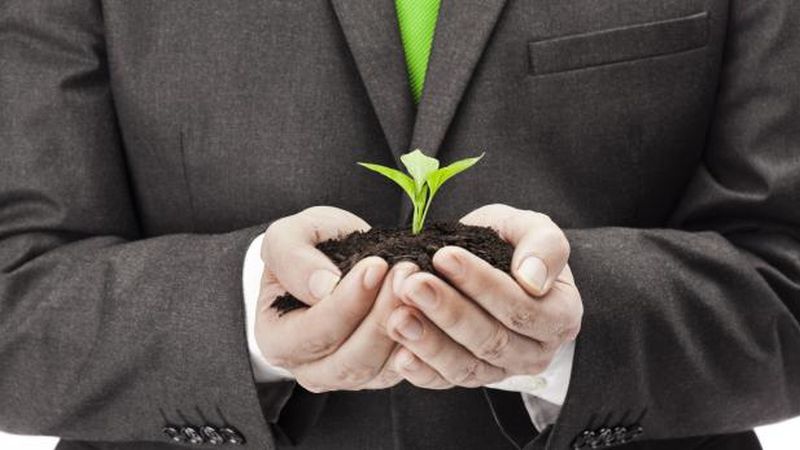
Many of these substances pose environmental dangers with considerable clean-up costs, or can cause irreversible environmental damage. Still, convincing the top management to invest resources to store hazardous materials safely can be quite difficult, especially when there are no accidents to amplify the need to exercise caution. That is why there are regulatory bodies that impose requirements and standards, and of course, sanctions.
Protective Equipment and Safety Measures
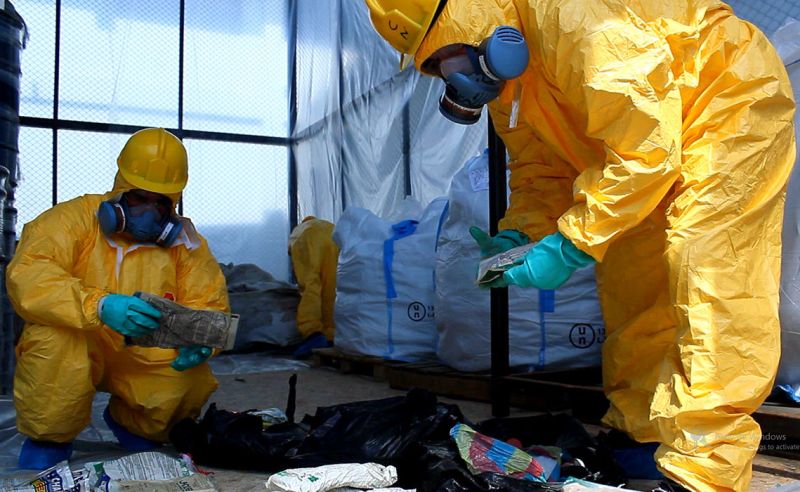
The Occupational Safety and Health Administration has set around 500 PELs (permissible exposure limits) in order to protect the workers against the health effects of exposure to hazardous substances. Usually, PELs are 8-hour time-weighted averages (TWA); however, Ceiling and Peak limits have also been established. <
Unfortunately, there are many substances for which OSHA still does not have workplace exposure limits, and many of the existing limits are outdated. However, there is a list of alternate occupational exposure limits that can be used to protect the staff.
Also, the worker’s exposure to toxic chemicals can be reduced through the means of effective engineering and work practice controls, and if they are not instituted or are currently being implemented, respiratory protection should be used with no fee for the workers.
Depending on the substance in question, adequate personal protective equipment (PPE) should be worn by the workers, each with specific applications and use requirements. Personal protective equipment is divided into four categories b (Level A-D) based on the degree of protection it offers.